OXY-FUEL COMBUSTION TECHNOLOGY FOR COAL-FIRED POWER GENERATION
- Atavika Chandan
- Oct 7, 2021
- 4 min read
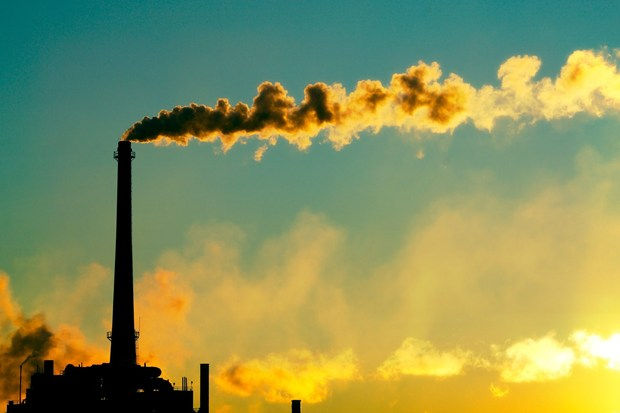
Introduction:
Energy production from conventional fossil fuel burning leads to the emission of greenhouse gasses, the dominant contributor being CO2. Although, it is a well-known fact today that the emission of these greenhouse gases is largely controlled by the implementation of alternative sources of energy, like the wind, water and sun and these renewable energy sources are expected to become increasingly essential for our future energy demand, but however, until these sources can reliably produce significant and enough amounts of energy, the immediate energy demand is likely to be met by conventional fossil fuel burning. From the past decade, the importance of coal as an energy source has gained renewed interest for its proven stability in supply and cost and it is, therefore, possible that coal will remain as an important resource of the energy mix in the foreseeable future. However, to maintain coal in the global energy mix in a carbon-constrained world, the greenhouse gas emissions emitted from its utilization must be reduced. Increasing reduction of greenhouse gas emissions can be achieved by the sequenced implementation of more efficient coal-fired power plants; however, to make a significant reduction in emissions, the CO2 obtained from coal combustion needs to be captured, stored and sequestered.
CO2 and the Flue Gas:
Many technologies are developing for CO2 capture and sequestration from coal fired plants. CO2 as a result of conventional combustion processes is present as a dilute gas in the flue gas (gas that emanates from combustion plants), resulting in very costly capturing using amine absorption. CO2 capture is more feasibly achieved from a concentrated CO2 stream, which can further be achieved by burning fuels with oxygen to get a sequestration-ready gas stream. This technique is termed oxy-fuel combustion, wherein the oxygen stream is usually diluted by recycled flue gas (RFG). There are no fully established plants using oxy-fuel combustion in operation. However, laboratory work and theoretical studies have given understanding of the relevant design parameters and operational issues.
Oxy-fuel technology description:
Conventional pf fuel-fired boilers use air to heat while nitrogen from the air (approximately 79% by volume) reduces CO2 emissions from flue gas. The transport of CO2 from such purified compounds using amine extraction is very expensive. During an oxy-fuel combustion, the mixture of oxygen itself is more than 95% pure and the recycled flue gas is used to heat the fuel. By recycling flue gas, a gas containing CO2 and water is produced, ready to be extracted without the removal of CO2 from the gas stream. Recycled gas is used to control the flames and to create a lost N2 volume to ensure that there is sufficient gas to carry the heat through the boiler.
Most experiments and studies on oxy-fuel technology are concerned about the use of coal-fired pulverised fuel boilers to produce a rich CO2 stream ready for sequestration.

Other studies have considered its application for oil and gas power plants. Recently, the driver for studies into oxy-fuel combustion is doubled:
(1) Obtaining CO2 gas stream suitable for sequestration
(2) The ability to reduce the cost of pollution control, with an emphasis on NOx.
A current emphasis has been to employ the technology to obtain a high CO2 concentration from coal combustion. Oxy-fuel burning has been illustrated at pilot-scale and CO2 formed during gasification is currently available for enhanced oil recovery (EOR), particularly in the United States.
A schematic of a pf coal fired oxy-fuel boiler is shown in figure below. Oxygen is extracted from air and then mixed well with a recycle stream of flue gases from the boiler. Fuel is ignited in the resulting gas stream and the flue gases are recycled partially. Water vapour is condensed from the flue gases to make a stream of high purity supercritical CO2. Oxy-fuel burning and CO2 capture from flue gases is a near-zero emission technology that can be converted to both hot and existing coal-fired power stations.
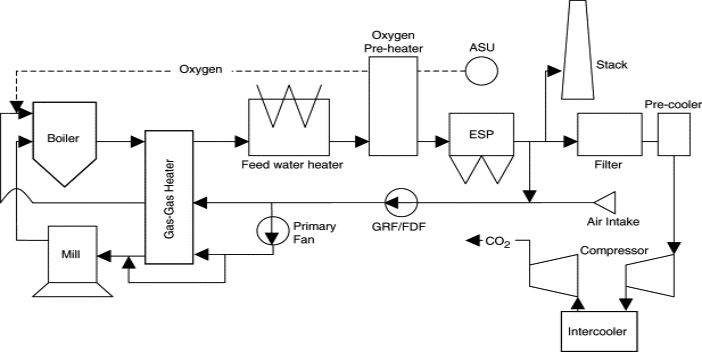
In oxy-fuel technology the carbon dioxide concentration in the flue gas is increased from approximately 17 to 70% by mass. The carbon dioxide can be then captured by cooling and compression for subsequent transportation and storage. In this form oxy-fuel heating involves the modification of standard coal pf technology to include oxygen separation, flue gas recycling, CO2 compression, transport and storage. Though, the addition of these operations do bring possible reduction in availability.
Conclusion:
After initial introduction in 1982, oxy-fuel combustion for pulverised coal combustion was researched as a way to supply relatively pure CO2 for Enhanced Oil Recovery. Even after these research efforts, this technology did not get a pick up on a large scale for this application. But, the increase in the awareness about greenhouse gas emissions into the atmosphere has revived the interest in this technology, with a dual focus:
1.The generation of a comparatively pure CO2 for sequestration
2.The potential to scale back pollutant emissions, especially NOx.
Research into oxy-fuel combustion has not been limited to the development of new plants that have the advantage of smaller flue gas cleaning equipment, but has also included prototypes of existing plants, particularly interesting for reducing greenhouse gas emissions from existing power generators. Moreover, the following issues have been identified for oxy-fuel combustion: (1) Heat transfer, (2) Environmental issues, like gaseous emissions, (3) Fly Ash related issues, and (4) Combustion- ignition and flame stability.
However, the techno-economic studies made a statement that oxy-fuel combustion is a cost-effective and efficient method of CO2 capture. More importantly, the studies indicate that oxy-fuel combustion is technically feasible with existing technologies, declining the risks associated with the implementation of newer technologies.
By Atavika Chandan
chandanatavika@gmail.com
Comments